Paper Makes a Poor FCA
Your typical FCA report binder contains 1-2 pages for each asset that includes photos of the asset and the data collected on it. There’s also usually a summary report that highlights the main things you should spend money on. The entire report could be well over 20,000 pages long. There’s so much useful data – but how are you supposed to navigate it? Imagine trying to find the page for a single air handler among all that information. The majority of the data is inaccessible because it’s so difficult to sort through, making it ultimately unusable.
Here’s the dirty secret of paper FCA reports – most people only look at the capital expenditure recommendations. The remaining thousands of pages in those binders just sit on the shelf as a shrine to all the hard work that was done. The binders are like a status symbol – the more binders, the more expensive the FCA must have been.
Sure, FCA providers may use digital tools like Excel, Word, or other programs to create the report, but the end result is still a printed end product that becomes a paperweight – and eventually ends up in the trash can.
At the end of the day, printed FCAs aren’t all that helpful to anyone. The architect or engineer conducting the capital needs assessment has to re-do all their work from scratch every time a new assessment is needed. Meanwhile, the building owner is left without much usable data or insights.
Read More: Facility Condition Assessment Checklist: How to Index Your Building
The Current System is Broken
The traditional way of doing FCAs is flawed in large part due to bad facility data and complex, poorly implemented facilities management software.
Most facility teams don’t have good facilities information to begin with – which makes it nearly impossible to create a truly accurate FCA. The building team may have a CMMS that records preventive maintenance history. But oftentimes, reactive maintenance history is a lot harder to track down.
Does this hypothetical situation sound familiar? Say an FCA engineer wants to know the complete maintenance history for air handler unit 62. He asks the facility team for the CMMS export on that asset. But that only shows some of the preventive maintenance history, no reactive maintenance. That’s because whenever air handler 62 has been serviced, it’s been treated as a work order issue instead of an asset-specific issue. Occupants complain that the room air handler 62 services is always too hot, so the maintenance team resolves the issue and closes the work order. But that maintenance isn’t associated with air handler 62 in the system, so the FCA engineer (and the building’s facility team) don’t know that maintenance was done on that asset when it comes time to review the history. Multiply that by the thousands of assets in your building and you see how difficult it is to get an accurate read on what’s happening.
Another problem we see that prevents good FCA results is facility management systems that are so complicated that people don’t use them. Say you want to associate a photo with an asset in the system. Seems easy enough – until you realize the asset isn’t named correctly, so you can’t even find it. And even if you try your best to associate it with something, you may misassociate the data, because you’re looking for an air handler unit on the roof of building 2. Well, there are 12 air handlers on that roof. How can you be sure you got the right one if they’re not put into the system correctly?
Many legacy systems are complex and not always implemented correctly. As a result, you can’t necessarily find the unique asset that you actually need to find to make that system work.
Good data and good tools can completely reform how we do facilities management and FCAs.
Read More: Give Your Clients an FCA They’ll Actually Keep Using
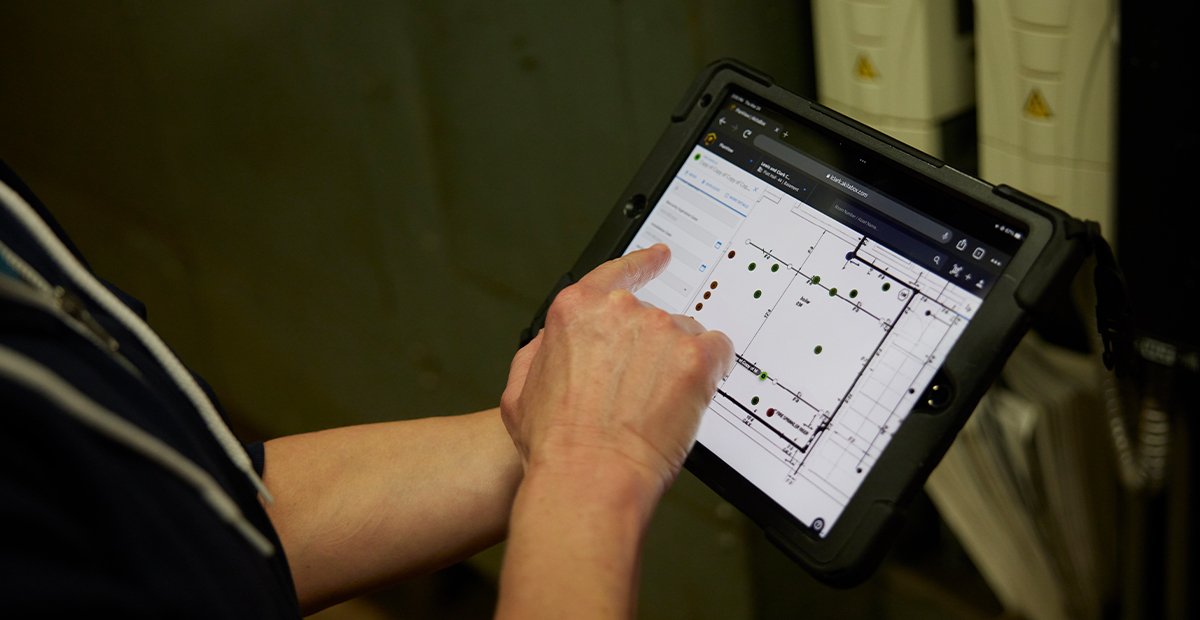
We All Deserve Better FCAs
Today’s FCAs exist to show you how to spend capital in terms of replacement cycles and your facility as a whole. It’s a very reactive way to spend capital. We let assets deteriorate and then bring in an expert to tell us where the worst holes are so we can go patch those first.
What if, instead, you could know BEFORE the asset fails (with predictive data) and take proactive steps to address it? Being predictive and proactive means spending more time maintaining the assets where that maintenance has a real impact on your dollars. No more spending time and wasting money on items that aren’t impacting that end capital expenditure.
Let’s hop in our time machine and get a look at the future of FCAs and facilities management: live diagnostics.
Think of a Toyota Prius with the dashboard monitor. You can see all four tires and their tire pressure in real time on the screen (among many other things). As soon as your tire pressure drops even 2 psi, you’ll see it right away. So you can remedy that before your tire drops 20 psi and becomes visually flat.
That’s the difference live diagnostics makes. Do you want to know when your tire starts losing air? Or would you rather wait until it’s visually low on air and you’re already damaging the outer wall of your tire? I know what I’d choose.
The same concept of live diagnostics can apply to buildings. Instead of waiting for an asset to become visually degraded, we’re going to be able to use our facilities data to tell us when it’s time to replace something.
Let me give you an example. You have an asset called Asset A that you’re keeping an eye on. With the right data, you’ll know how often you worked on it last year and how much time and money that maintenance cost, which lets you calculate the total cost of ownership. Say it’s $1800 and Asset A is a $2200 asset. Starting to get a little pricey to maintain it. Probably time to replace it.
Assuming you have redundancy for Asset A, you can decide to make it run-to-failure and stop preventive maintenance on it. You’ll buy another one, and if Asset A fails, you’ll just replace it. Now you’re not spending money and time unnecessarily when Asset A goes down. The day it fails, you can swap it out and be back in business.
This is predictive maintenance in action. It’s like a live feed telling you “Hey, you’re starting to spend too much money on this asset, you need to take action.” You can set parameters that once this asset and this risk level reach a point where maintenance becomes more than 20% of total replacement costs in a single year, it throws the red flag to move it from a preventative maintenance schedule into run-to-failure mode. THAT is maximizing your ROI.
Now your facility condition data is going to really work for you every day. Now your FCA becomes an opportunity for an outside engineer to come in and validate your data, ensure everything is still up-to-date, and give their expert opinion on any problem areas.
It All Starts With Better Data Collection
If you’re not ready to make the leap into fully digital FCAs, at least start with better data collection. Look into investing in a good data capture tool. It’ll get you standardized and doing things in a more electronic way. A data capture tool also lets you log photos and notes in a meaningful way against a floor plan.
Whether a data collection tool seems like a baby step or a huge leap to you, better data collection moves you into a world where your underlying FCA data is no longer thrown away. Now you’re putting the data in a spot where it can live on. That’s key, because now if you want to have an ongoing relationship with it, it’s so much easier to update it and keep that data alive.
So what’s your current data collection process look like? Would you like to do data capture better?
AkitaBox is first and foremost a data capture tool:
- Map your assets to your current floor plan
- Add photos, notes, manufacturer info, and more to each asset
- Text recognition lets you take photos of asset tags vs. manual entry
- Create custom fields to track the information most important to you
- Keep all of your asset data in one place
- Easily share data between teams and departments
And that’s just the start of what it can do. Discover how AkitaBox software helps you build a foundation of dependable data that can launch you into a future of better facilities management.