If you want to optimize asset performance and ensure efficient operations, you absolutely need to understand the asset lifecycle. Every asset – from the boiler in the basement to the shingles on the roof – has an optimum operating period of peak performance. After a certain period of use, wear and tear takes its toll as the asset ages. Eventually, every asset must be replaced.
Knowing where each asset is in its lifecycle helps you avoid unplanned downtime and stay ahead of replacements. Making smart decisions at every stage of the asset lifecycle helps you improve asset efficiency and saves your organization money over the long run. So, without further ado, here are the four key stages of the asset lifecycle and how you can use them to your advantage.
The 4 Asset Lifecycle Stages: Explained
Stage #1: Planning
The planning stage determines the current condition of equipment and other building assets and the most cost-effective means of moving forward. A building manager may:
- Assess whether or not current equipment meets production needs
- Ensure that necessary resources are available for use
- Identify which assets are underperforming or unnecessary to operations
- Check that equipment is receiving proper levels of maintenance
- Estimate funding required to procure a replacement asset
If a machine or piece of equipment is underperforming, the next step is to research available replacement options, make comparisons, and conduct demos or trials (if applicable).
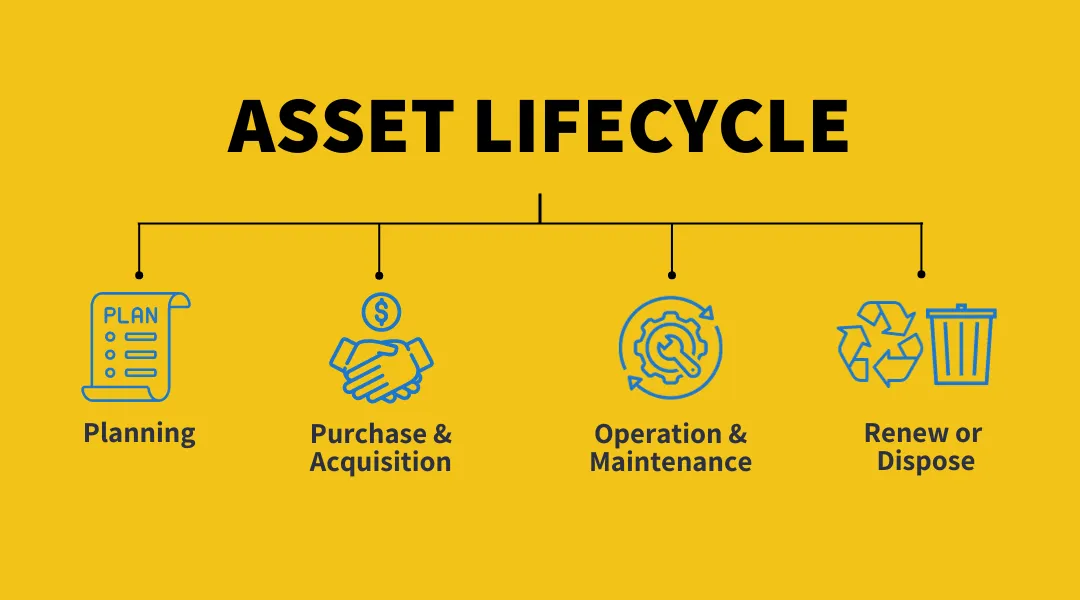
Stage #2: Purchase and Acquisition
This stage is about defining the costs and requirements of purchasing the asset – with the goal of making the acquisition as cost-effective as possible.
It’s important to take into account the asset’s initial investment costs as well as the its total cost of ownership. Finally, the asset is installed and added to the organization’s asset management software.
Stage #3: Operation and Maintenance
This is typically the longest and most substantial stage of an asset’s useful life. In this stage, operation and maintenance activities are performed and tracked, typically in a software platform. Building management teams focus on keeping the asset in good working condition to ensure efficiency and productivity, using preventive maintenance programs, regular inspection schedules, specialized cleaning routines, and regular routine maintenance.
The operation and maintenance stage can be broken down into 3 Rs: Repair, Rehabilitate, and Replace. In other words, assets should be monitored to ensure that repairs, parts replacements, and adjustments are done in a timely manner to ensure ideal functionality.
Stage #4: Renew or Dispose
As long as an asset is functioning correctly, it’s within its useful life. But there’ll come a time when the asset’s performance significantly deteriorates. Assets that are approaching (or exceeding) their life expectancy will experience age-related wear and tear or outright failure. Equipment that fails to meet production quotas or efficiency standards ultimately impacts an entire organization’s success. In this situation, it’s time to renew or dispose of the asset.
In the wake of asset failure, asset management software can provide the asset lifecycle data needed to inform the best way forward. A good rule of thumb is that if the cost to repair an asset is more than the cost to replace it, it’s most cost-efficient to dispose of (aka “decommission”) the asset. Once an asset is decommissioned, that asset’s lifecycle is over and a new asset’s life begins again at stage 1.
Why Does Asset Lifecycle Management Matter?
Properly managing the lifecycles of your equipment has a significant impact on your organization’s efficiency, cost control, and overall performance.
- Clearly defines your assets and their conditions. Good asset management software lets you record the installation date, condition, and cost-effectiveness of each piece of equipment. This data can be used to forecast an asset’s estimated useful life and total cost of ownership.
- Supports a proactive approach to maintenance. Asset lifecycle management helps a business actively manage the physical health of its machinery. Proactive maintenance enables organizations to better predict future scenarios, plan for asset failure, and take well-planned steps regarding maintenance and eventual replacement.
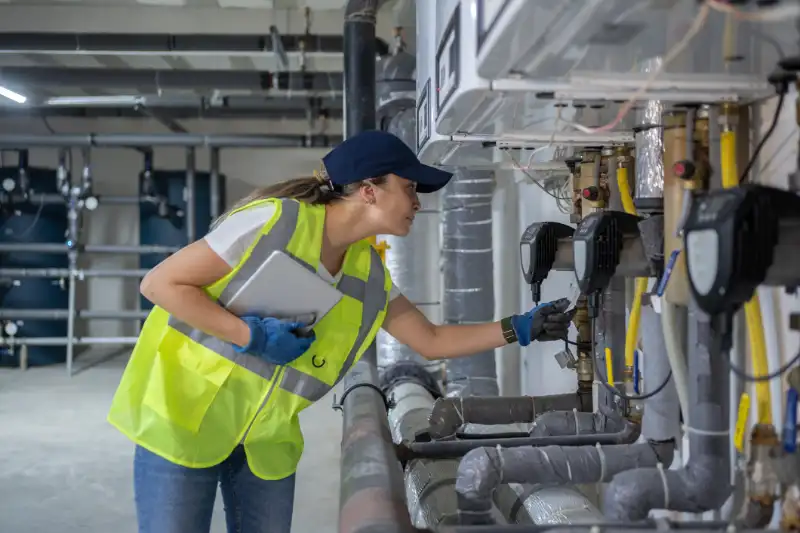
- Supports regulatory compliance in your organization. With the help of facilities management software, your team can collect and use valuable lifecycle data for each critical asset. This way, your team can catch existing problems before they become a compliance issue with regulatory organizations (like OSHA) or accrediting agencies (like the Joint Commission).
- Helps prioritize equipment and machinery replacements. Creating and maintaining a capital budget is an important part of managing a building. By staying up-to-date on asset conditions and life expectancies, your team can more accurately forecast funding needs and ensure maintenance reserves are sufficient.
How to Calculate the Real Costs of Asset Ownership
Have you ever wondered how much it truly costs to purchase, operate, maintain, and dispose of an asset? These are good metrics to know, especially because your organization will invest a significant amount of money into equipment during years of ownership. Download the Life-Cycle Cost Analysis Formula, a guide for calculating the lifetime cost of a fixed asset, to discover the true cost of owning each of your assets.
Read Next: How to Calculate Equipment Depreciation Life and Why It’s Important
Make the Most of Your Assets’ Useful Life with AkitaBox
Using AkitaBox Pulse, you can manage assets, maintenance, assessments, inspections, and capital planning in one platform. Enjoy an always-current view of your assets’ conditions. Easily access all of that valuable facilities data to make day-to-day decisions and determine long-term strategies.
See how AkitaBox Pulse could help your team by requesting a customized demo today!