Beyond the Basics: 3 Questions to Take Your Preventive Maintenance Strategy to the Next Level
You’re tired of beginner-level preventive maintenance (PM) information. You want to take things up a notch. Play in the big leagues. Run with the big dogs.
You’re in the right place. We’re going to discuss 3 advanced-level concepts that’ll help you take your PM strategy to the next level.
But before we go any further, let’s make sure you already know the essential information upon which any good PM strategy depends:
- What assets do I have?
- How long does it take to PM each asset?
- What expertise level is needed to PM each asset?
- Which assets are most essential to my organization’s mission and should be prioritized for PM?
Don’t know those answers yet? That’s ok. Our Step-by-Step Guide to Building a Preventive Maintenance Plan will help you get there.
If you do feel confident you can answer those questions, then keep reading – you’re ready for more!
Do I know what PM work is (or is not) getting done, and is there a strategy behind it?
In my experience, I’ve noticed that a lot of facilities managers operate under the assumption that they don’t have enough staff to do all the PM work. They take an approach of “well, let’s schedule every PM task, and if we get to it, great – if we don’t get to it, darn.” In their minds, the fact that they’re PMing anything is good, because they weren’t doing PM at all before.
Yes, doing PM is good, but many facilities leaders aren’t being strategic about it. Quick: do you know which PMs are getting done and not done in your organization? Do you really know? Do you know why it was or wasn’t done? Do you know the last time PM was done on that asset?
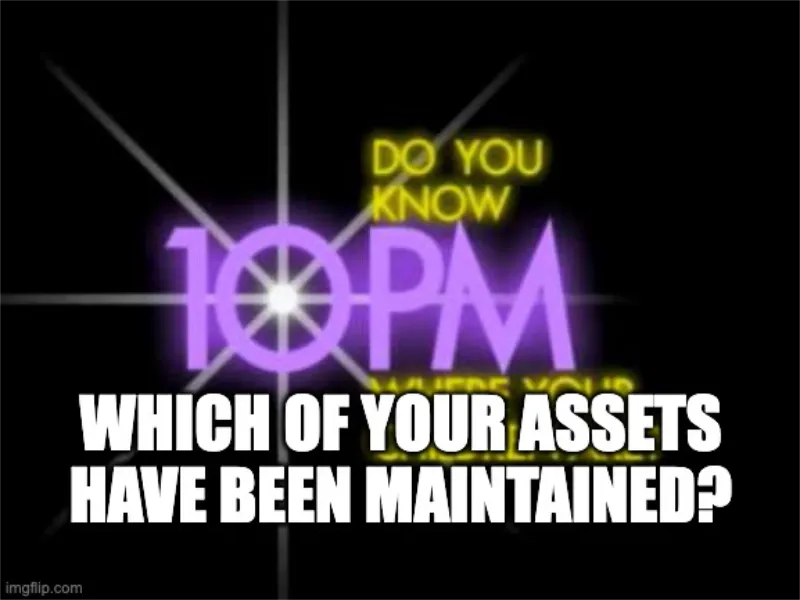
A truly next-level PM program is a strategic one. Yet many organizations don’t focus on their PM strategy because they know they don’t have enough labor to do it well and because reactive maintenance needs take precedence.
Recently I had a conversation with a facilities leader about how PM work orders are created in AkitaBox. He asked why AkitaBox creates a PM ticket if the previous PM ticket hasn’t been completed yet. Why can’t the software simply not create the next PM work order until after the previous one is finished?
I can see where he was coming from. They were dealing with too many PM tickets being scheduled. If the software just keeps creating PMs when they should be created based on the asset’s PM schedule but some of the tickets get skipped or delayed, now you have multiple tickets for the same work. However, if you were to delete (or not create) those extra PM work orders, now you don’t know what you’re not doing. How do you know what’s getting done and what’s not getting done?
Sure, we can build software that would make those extra PM tickets go away, but then you’re not forced to make a strategy. You’re not asking yourself why you’re skipping some PM tickets and the risks associated with doing that.
Say you have 6 cars in your fleet. Each one needs an oil change every 3,000 miles. But you only have the staff to do oil changes on 3 cars every 3,000 miles. So which 3 don’t get done? Without a strategy, you don’t get to choose. You aren’t even able to be strategic about it. You’re leaving it up to chance. It might be the last 3 cars that rolled through the garage didn’t get oil changes, but they were the ones that needed them the most. But because you’re just leaving it up to your techs to decide and there’s no strategy around it, you shouldn’t be surprised when you get poor results.
What if you created an actual strategy for your cars’ oil changes? You already know you only currently have enough manpower to do oil changes on half of your fleet cars every 3,000 miles.
So, you could:
- Hire more staff
- Do oil changes on the first 3 cars one cycle and then the other 3 cars the next cycle
- Track each vehicle’s mileage and wear-and-tear and prioritize the cars being used the most
Approaching PM strategically is absolutely possible. We have more visibility into our facilities than ever before. We have the ability to track what PM work we’re doing and not doing in today’s software tools. We can track our asset performance and lifecycles. All this data empowers you to make wise PM decisions.
For example, you could confidently decide not to do PMs on certain assets because you’re not actually seeing any decrease in end of useful life. You could point to your data that says pumps under a half horsepower are only $300 and it’s not worth the labor to even go look at the thing. When it breaks, it breaks, and you’ll replace it. By making a data-backed decision and continuing to monitor the data around those pumps, you can prove that you actually didn’t diminish anything by not doing PMs on this type of equipment. That’s powerful.
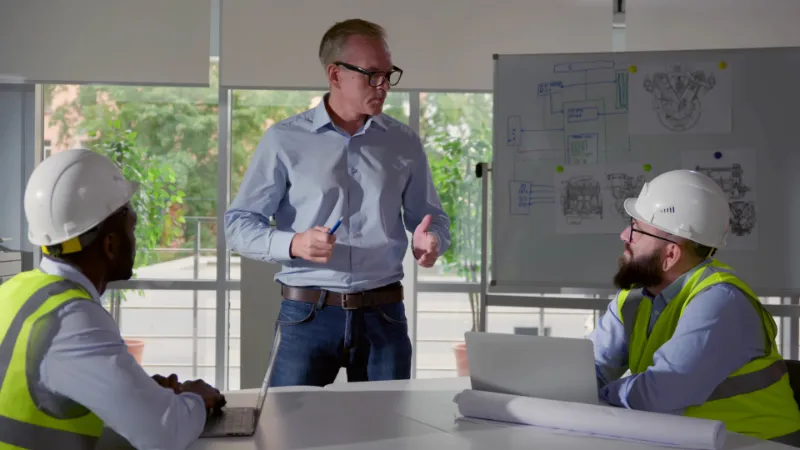
Or consider another scenario. You discover that a certain manufacturer performs better than another – which can influence future construction. Say you don’t PM those pumps from the example above and you notice that one manufacturer’s pumps don’t have a change in end of useful life, but another manufacturer’s pumps fail in half the time.
Think how valuable that information is. It can help you pick winners and losers in terms of equipment type, manufacturer, model number, etc, for your next build. As a result, your new construction is more operationally cost efficient, because you’re using true operations data from the back end to choose which assets go into your new building. That’s bringing your facility’s lifecycle full circle.
Should I hire more PM help internally or use third parties?
Chances are, you don’t have enough people to do all the PM work that could (or atleast should) be done to your assets. In that case, you can make some decisions. Maybe you can choose not to PM certain assets or do less PM work on some assets. (Of course, you want to make these choices strategically – as we addressed in the section above – instead of leaving it up to chance what does or does not get done). But even then, you’re most likely still going to come up short on people.
So then the question becomes: do I hire more people internally or use a third party? Both options have pros and cons.
Having your own internal experts on staff is great – except they’re not on-call 24/7. They can do alot of PM work that you would have to hire somebody for otherwise, but they’re only around a limited number of hours a day.
Third-party workers can be available 24/7 (depending on your agreement), but they may not understand the unique ins and outs of your facilities as well as an in-house team member. In addition, there is often high turnover within those third-party contractors and it can be challenging to manage a constant stream of new people going in and out of your buildings.
Secondary to the question of whether you decide to hire more staff or use contractors is: how balanced is my PM work throughout the year?
For example, is all your HVAC PM work spread out throughout the year, or is it really heavy during just two months? If all of your PM work needs to happen in two months, one person couldn’t keep up. And if you hired enough people to deal with all the demand in those two months, you wouldn’t have anything else for them to do the rest of the year. In that situation, maybe it makes sense to supplement your HVAC engineer with a service contractor during those two high-load months.
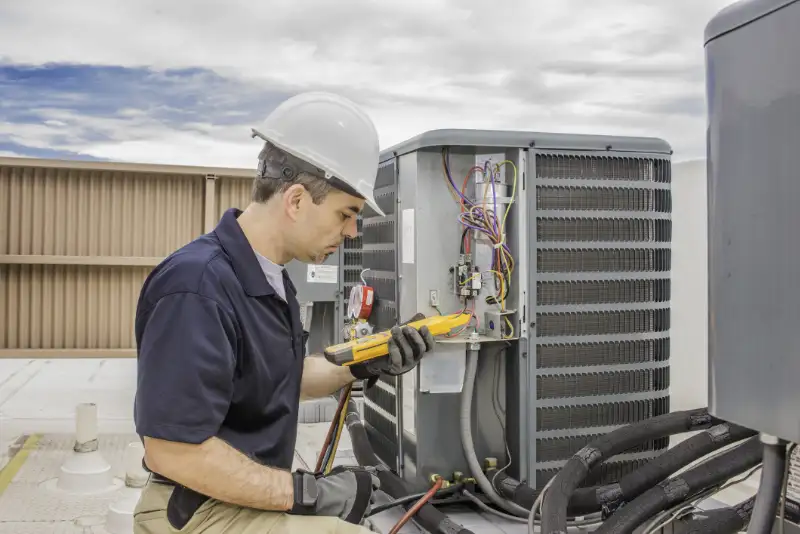
And finally, you need to ask yourself: what are the skillsets of my in-house engineers? Because that will impact what type of work your team can do and what type of work you’ll need to hire out for.
If your in-house HVAC engineer is a 30-year veteran, they should be doing high-value work and you can bring in outside contractors for basic PM work. On the flip side, if you’re HVAC tech is straight out of the trades and just trying to get their feet underneath them, maybe it’s best to have them focus on filter changes and other low-value tasks and put some money towards hiring experienced third-party engineers for the high-value work.
Those types of decisions depend on who’s sitting in the seats on your bus at your organization and what strengths or weaknesses that gives you.
So, in review:
- Do I have enough people to do PM, or don’t I?
- If I don’t, what PM will I not do?
- Then, who am I going to bring in to help?
It’s actually not super complicated if you break down your PM strategy by system. If you look at HVAC all by itself, for example, it’s a really easy equation:
- How many people do I have that can PM my assets?
- How many hours do they have available to spend on PMs?
- How many hours would it take to do PMs on all the pieces of equipment that I have?
- What’s the difference between the number of hours needed to do PM and the available labor hours you have?
- Do I have too many people or too few people?
Once you determine that you have too few people to PM everything you own, you decide whether to not do some PM or hire yourself more help (either internally or as an outside contractor).
When should I stop PMing an asset?
Every asset eventually reaches the end of its life. But at what point does it no longer make sense to maintain that asset?
That’ll depend on questions like:
- What is it and where is it?
- How much money have I already spent on it?
- Is it worth spending one more dollar on it or not?
- How easily replaceable is it?
- Is it already really energy inefficient or will it become even more energy inefficient if I stop PMing it?
While you need to look at each asset individually when making this decision, it’s a good idea to develop some organizational criteria to guide you. Unfortunately, none of us have unlimited money to replace every asset the moment the data says to replace it. So what do you do? Have you openly had a conversation inside your organization about what your replacement decision-making strategy and threshold should be?
I think we’ve become so reactionary that we’ve basically chucked the idea of being thoughtful about asset replacement out the window. So many of us have never even had those internal conversations about when we should replace a piece of equipment. The default has become that when something breaks, we replace it, and until then we keep maintaining it.
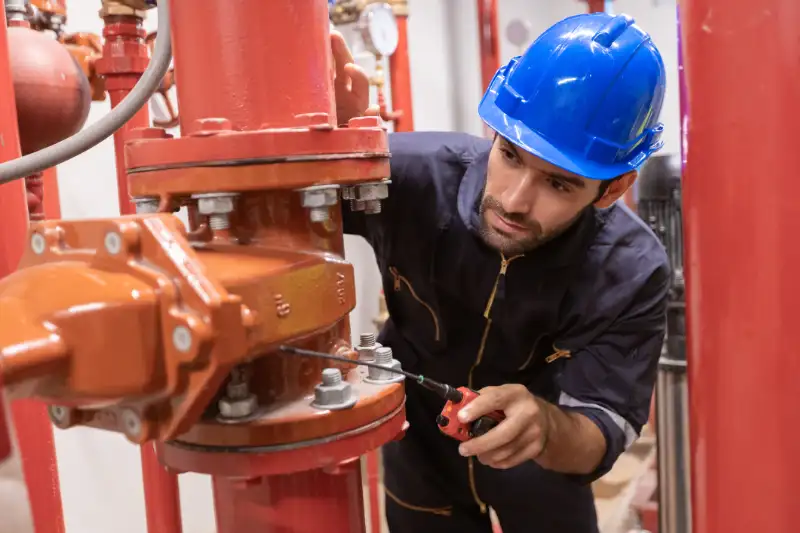
But just because something is still running doesn’t necessarily mean you should keep maintaining it. Maybe you should stop PMing it because it doesn’t make sense from an energy perspective. Or you’ve already spent enough money on maintaining it to replace it three times over.
I’ve found that people tend to overcomplicate this because there are a lot of different systems that interact in a facility. But if you break each system down individually, it’s really not that hard of a decision to make.
For example: say you have this many light bulbs. Your light bulb uses this much energy – and that means you’re spending $10,000 a month. If you decided to spend $10,000 to replace all your light bulbs with LED bulbs, you would save yourself $9,000 a month in energy costs. You’d have that $10,000 paid back in one month and then you’d start making money. That makes a lot of sense, right?
You can boil down seemingly complex situations into more clear cut equations when you look at individual systems. But it can be difficult for facility managers, CFOs, and the like to look at everything individually because all the facility information is flowing to them all at once. It can get overwhelming pretty quickly. That’s why it’s so important to have a set of decision-making criteria for when to stop doing PM or when to replace an asset.
Conclusion
So there you have it – 3 key questions that’ll guide you towards a stronger, more strategic PM plan. I’ll leave you with one last thought. You don’t have to answer all these PM questions on your own. Facilities management and asset data management software is getting better all the time. Lean on technology (including AI) to help you collect and analyze the data you need to answer PM-related questions.
Here at AkitaBox, for example, we’re leveraging AI to streamline and speed up asset data collection, analyze facilities data for trends, and even suggest actions to take. Just set up a short demo to see how we make PM easier for you.